As I began to pull all the materials together and train the team, I quickly realized that I could be as passionate as I wanted to about hospital safety (yes, I actually was, I know … it’s a little strange) but if the practice as a whole didn’t have an overall compliance culture, we were doomed to fail.
First, demonstrate a commitment to compliance
Let’s break this down – what exactly does a compliance culture look like? There are several facets: commitment from leadership, empowerment and education of staff, integration into daily operations and accountability. Beginning with leadership, it’s a no-brainer that managers and owners should lead by example and communicate the importance of safety to teams.
1. Define clear expectations by writing a code of ethics and compliance policies that outline the expectations for staff: how to handle different scenarios, reporting and investigation procedures.
2. Appear visibly and actively engaged by making frequent rounds to actively observe safety practices can help as well. This isn’t intended to be an activity where team members feel they are being “spied on” or will be fussed at if they are doing something unsafe; instead, conversations around safety should be had privately and discreetly along with a tone that’s concerned rather than disciplinary.
3. For any accident investigations, safety committee meetings and training sessions, leaders should also be present to demonstrate their commitment to continuous improvement and desire to openly communicate with staff.
4. When team members demonstrate exemplary safety practices, reinforcing the importance of safe behavior and motivating others through public recognition (assuming the individual is okay with this type of acknowledgement) can be another way for leaders to step up to the plate.
5. Lastly, when employees report safety concerns or incidents, there should never be fear of retaliation (that means no sighs of exasperation when someone is bitten by a cat for the fifth time in a week – this is an opportunity to be supportive in the moment, get them the care they need, then reassess your training plan and next steps).
Second, begin safety training
Empowering employees begins with thorough training. Training doesn’t have to be in-person; it can be through online courses and should include all general industry requirements (e.g., exit routes and emergency planning, PPE, fire protection, first aid, hazard communication), as well as relevant occupational health and environmental controls (e.g., occupational noise exposure, radiation) and toxic and hazardous substances (e.g., formaldehyde, ethylene oxide).
Be sure to look up your state’s specific requirements when it comes to safety training to ensure you have all your bases covered.
Once employees have completed their training, document what training they have attended and when; if desired, you can have a log where team members also sign off on their training, but this is not required.
Consider how to make reporting processes and open communication as easy as possible for your employees. This may include an anonymous reporting channel. Empowerment may also be through the establishment of a safety committee and safety-specific roles. This provides employees with the opportunity to take on additional responsibilities that can help boost their resume, may feed an interest of theirs, or if you choose, be associated with a compensation increase.
Third, make safety part of every day
Integrating safety compliance into daily operations can help make it not appear to be an isolated activity. When considering a new workflow or a new treatment plan, looking at it through an employee safety lens can help keep workplace safety as an everyday part of practice decision-making.
Beyond integration, accountability at all levels is crucial. This means veterinarians don’t get a pass simply because of their role – all team members are held accountable for following safety policies, which ensures a sense of fairness and consistent enforcement.
Compliance can also be made much easier when tools and software are utilized to automate related tasks, provide reminders for reassessing SDSs, administer training and much more. You also don’t have to wait for an inspection from a Compliance Safety and Health Officer (CSHO) with the Department of Labor/Occupational Safety and Health Administration to let you know where your practice falls short. Perform regular walk-throughs to catch areas that need to be corrected, and quiz your team to ensure they know how to access all the necessary safety-related resources.
Creating a culture of compliance certainly doesn’t happen overnight, but with time you can begin to cultivate a team that prides itself on caring for one another’s safety and takes shared responsibility to exceed regulatory expectations.
For more about compliance, visit our consolidated compliance resource page.
Share
Related blogs
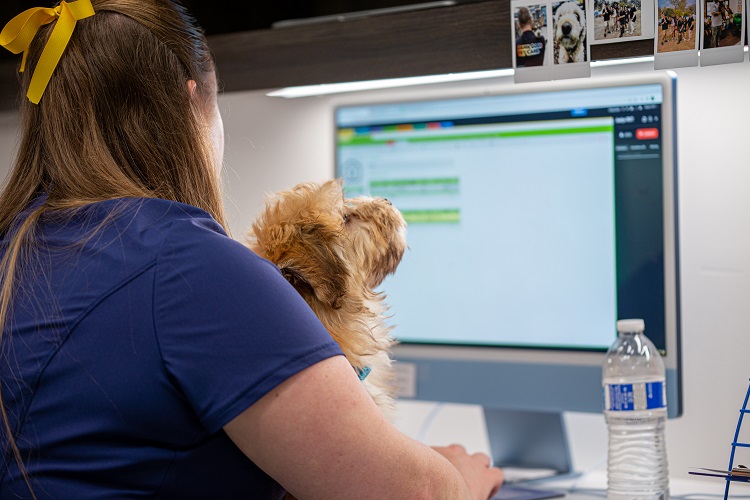
Top 7 Questions From our Impact of OSHA Changes Webinar
If you missed our Impact of OSHA'S Hazard Communication Standard 2024 webinar, don't worry - we got you! In this post, we're reviewing seven of the most-asked questions, as well as outlining what has recently changed.
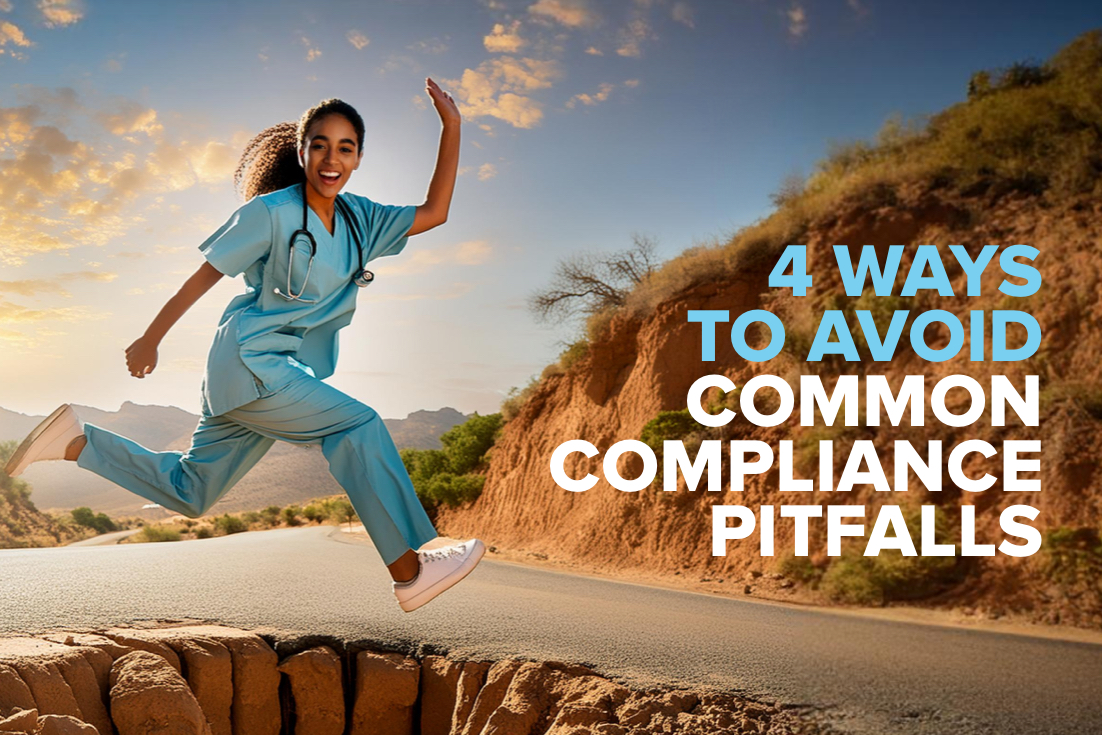
4 Ways to Avoid Common Compliance Pitfalls
We’ve got recommendations to help you avoid the most common OSHA compliance pitfalls and safeguard your employees’ health and wellbeing.
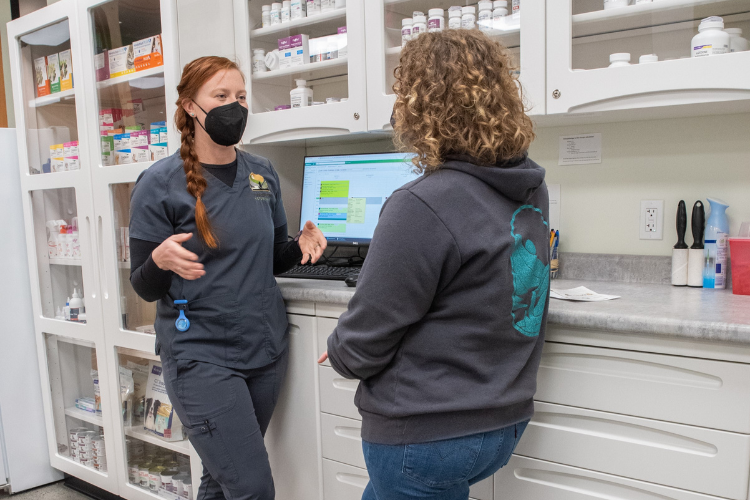
8 Frequently Asked Questions about Safety Data Sheets, Answered
It can be difficult and tedious to remain compliant with OSHA standards when it comes to safety data sheets. To help, we gathered 8 of your most frequently asked questions about SDSs, and broke down the answers here!