If you missed our Impact of OSHA’s Hazard Communication Standard 2024 webinar, don’t worry – we got you! Here, we’re outlining what changed as well as the most-asked questions.
Veronica Marrero, director of professional services and regulatory operations for TotalSDS and webinar co-host, noted that SDS content requirements have also been updated. In general, the changes include an addition to the eye irritation category and multiple updates to the hazard categories for aerosols and flammable gases, additions of new hazard classes and prescribed concentration ranges.
“If you have any role in protecting workers’ safety and prevention of chemical exposure, then these updates are relevant to you,” said webinar co-host Rennee Karlik, senior regulatory compliance specialist.
“These updates will require a thorough review of your hazard communication programs, including updating safety data sheets, SDS management and ensuring that labels and secondary containers on site meet the new requirements. You’ll need to focus on the implications of these changes for product labeling and safety data sheets, particularly in relation to trade secret management and ensuring compliance across the entire supply chain.”
1. What is the timeline for the changes?
January 19, 2026
Manufacturers, importers, and distributors: compliance for substances July 20, 2026 All employers: compliance for substances
July 19, 2027
Chemical manufacturers, importers, and distributors: compliance for mixtures
January 19, 2028
All employers: compliance for mixtures
2. Where can the trainers get training or access resources to help with training the staff on these changes?
“OSHA provides a lot of resource materials. TotalSDS also provides the guidance to the appropriate materials for each kind of group,” Marrero said. “Use us as a resource! In addition to the osha.gov website for the Hazard Communication Standard.” Your Patterson territory manager and technology specialist are also available to help.3. How will practices know if they have the most updated SDS?
“A good indicator is if you go to Section 9 of an OSHA SDS that’s currently compliant with today’s standard, it will have ‘appearance’ as the first physical property. After these changes are effective, it will say ‘form’ and then ‘color,’” said Marrero.“That’s probably the first place I would go to see if those physical properties have changed. Also if there’s a difference in the header. If your old one says in compliance with HazCom 2012 and this one says HazCom 2024 – but they’re not all going to say that. So Section 9 would be the place I would go to.”
4. Does Patterson AutoSDS update the safety data sheets in their catalog or does the practice have to do anything for those updates to apply?
“The most up-to-date SDS will be the one that you retrieve,” Marrero said.5. What is the best way to have SDSs digitally available? Just the AutoSDS subscription?
“Yes. It’s a very easy-to-use system and it’s readily available and there’s a mobile app,” Marrero said. “That’s a great benefit – that the power can go out and if you can’t look at your computer, you can look at it on your phone, you’re still compliant.”More about AutoSDS can be found here.
6. Can practices expect that manufacturers will send the updated SDS forms if their products have been reclassified? Or do the practices need to research their product reclassification?
“As soon as there’s an update, they’re supposed to disseminate that information. I’m not saying that that’s going to happen. I would start bugging people – we do it all the time!” Marrero said.7. With AutoSDS, do practices still need hard copies? Should they also keep safety data sheets for products they no longer use?
“You’re not required to have a physical binder. I think the digital access, the way we work today, is by far the best. But if you want to have a central repository of a binder somewhere in your practice, that’s fine too. But you don’t need both,” Marrero said.Karlik noted, “You do need to keep an SDS for at least 30 years in your records, even if you’re no longer using the product. The biggest reason for this is in the event that there is a long-term or chronic exposure result from a chemical, there needs to be access to the documentation that was available to that employee at the time of exposure.”
Share
Related blogs
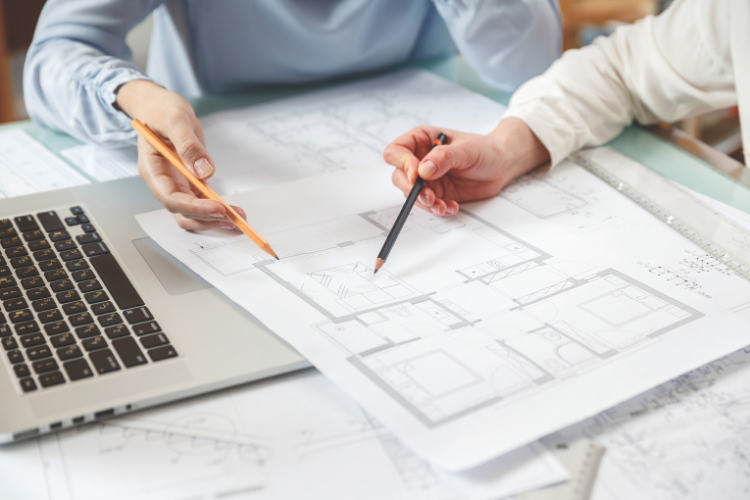
Design Solutions to 6 Pesky Practice Problems
Senior designer April Cuellar is part of a Patterson Veterinary Hospital Design team that advises on more than 300 clinics a year. She shares how design can help with six of the most frequent challenges practices face.
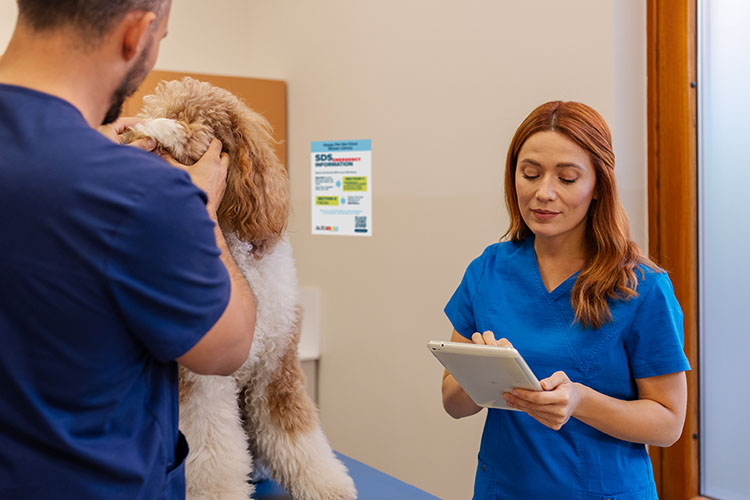
7 Resources to Help You Conquer Compliance
Terms like “OSHA,” “regulatory compliance,” and “hazard communication protocol” may seem intimidating, but by broadening your expertise in these key areas, you’ll find empowerment. From podcasts to webinars, these 7 resources will help you become a compliance champion.
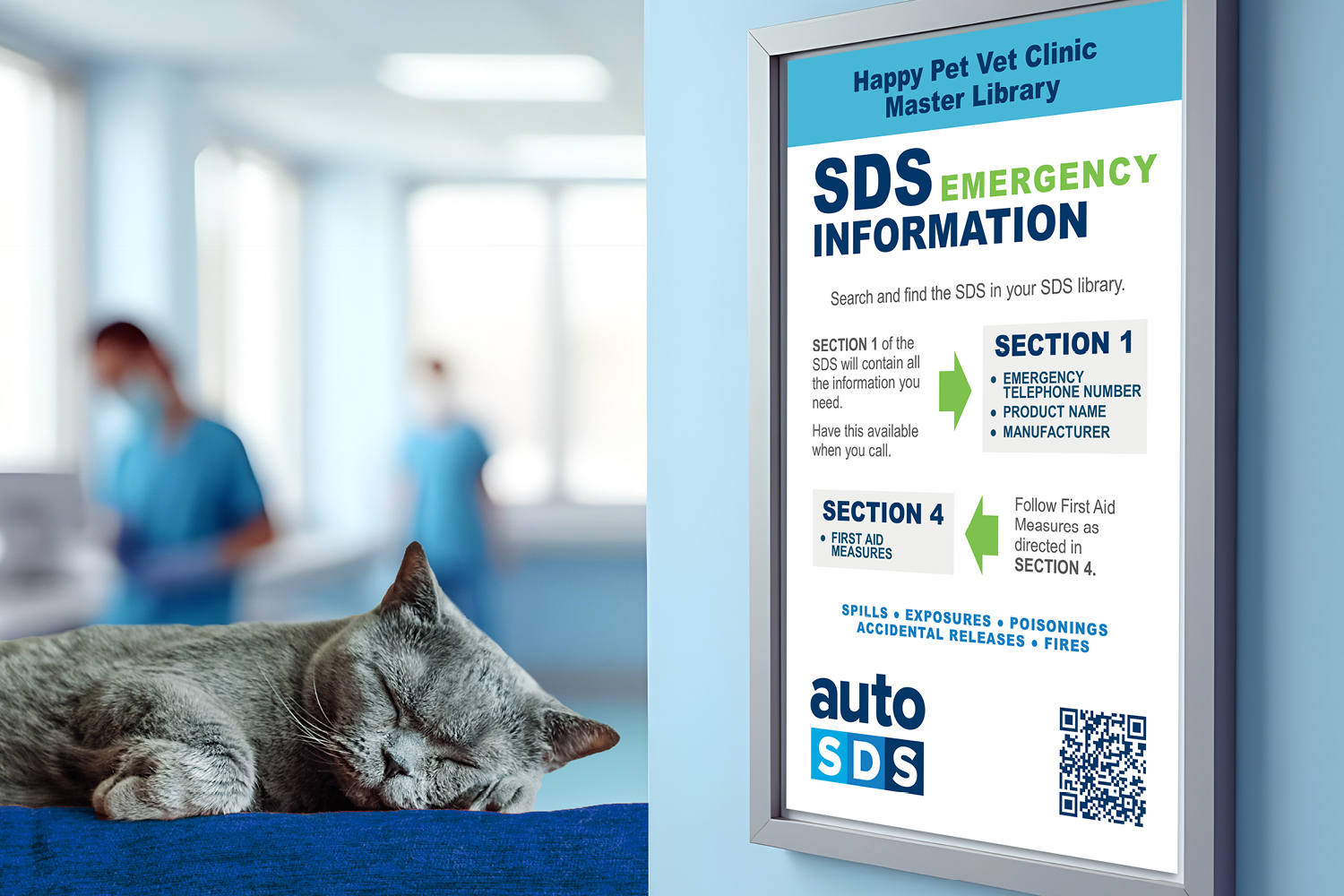
OSHA Compliance: Examining the Foundational Role of Safety Data Sheets
TotalSDS’s Alex Milan and Veronica Marrero offer an overview of the importance of safety data sheets, including two case studies that illustrate the risk of noncompliance. Finally, they share a compelling digital safety data sheet management solution.